WGU D471 OA Study Guide I - 2025 | Risks, Efficiency, and Cost Ownership📖
As a practical method supply chain management brings active movement to our world. The constant presence of your preferred snack next to other products on the shelf along with sudden product disappearances pique your curiosity. Companies persistently face supply chain risks while deciding between lean operation and agile manufacturing and conducting TCO evaluations to prevent unexpected financial consequences.
This article covers essential aspects of supply chain risks, manufacturing strategies, and cost analysis:
- Types of Supply Chain Risks: Supply chain risks include natural disasters (which disrupt operations), geopolitical instability (which can cause delays or shortages), cyberattacks (targeting data and systems), and supply risks (such as shortages or quality issues from suppliers).
- Lean and Agile Manufacturing: Agile vs. Lean: Lean manufacturing focuses on minimizing waste and improving efficiency, while agile manufacturing emphasizes flexibility and responsiveness to market changes. The key difference is that lean is process-oriented, and agile is adaptable to customer demands.
- Total Cost of Ownership (TCO): TCO is a financial estimate that calculates the total cost of acquiring, operating, and maintaining a product or service over its entire lifecycle, including both direct and indirect costs, to assess its true value.
Understanding these key principles is essential for students and professionals navigating supply chain management. Whether you’re planning to ace your WGU D471 OA or looking to future-proof your business, this guide will provide valuable insights in a clear, engaging way. Let’s dive in and make supply chain management a little less intimidating—and a lot more interesting!
How to Use This Guide for the WGU D471 OA Exam?📖
The D471 Global Supply Chain Management OA exam at WGU evaluates your understanding of supply chain risks, manufacturing strategies, and cost analysis. This guide simplifies the key concepts of types of supply chain risks (natural disasters, geopolitical instability, cyberattacks, and supply disruptions), lean and agile manufacturing (agile vs. lean), and total cost of ownership (TCO) to help you grasp the topics tested in the exam.
We also provide exam-style questions and practical applications to ensure you’re fully prepared for the questions on the WGU D471 OA exam.
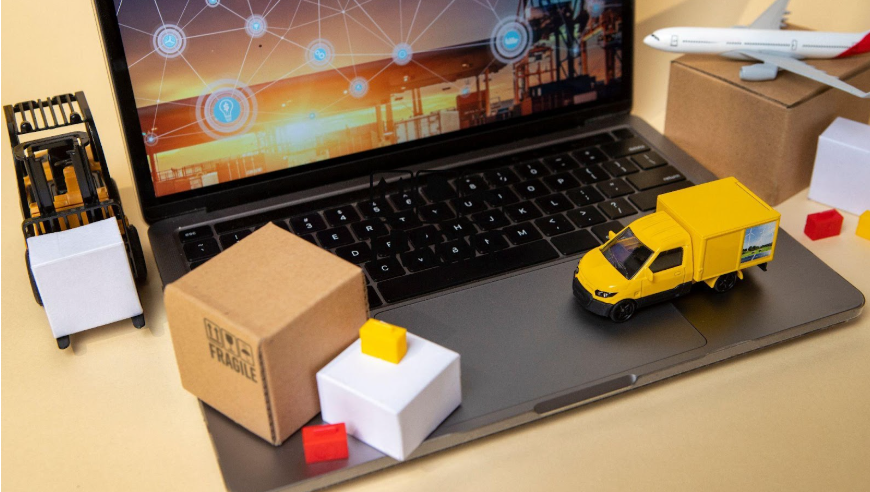
Understanding Supply Chain Risks For D471 OA📝
Companies within the supply chain field need to prepare for multiple operational events since they regularly encounter various challenges. Natural disasters along with political changes cyber threats and supplier malfunction threaten the stability of business operations. The following part presents an easy-to-understand analysis of these risks as well as protective measures for companies.
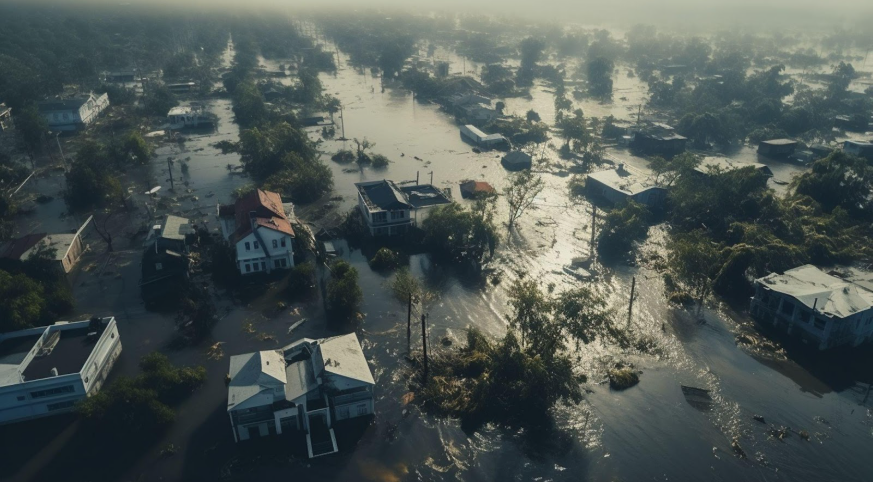
1. Natural Disasters and Environmental Risks
The stoppage of a factory that manufactures cars due to either a flood disaster or earthquake occurrence proves this argument. A natural disaster leads to such supply chain risks. The destructive forces of hurricanes together with droughts and wildfires introduce manufacturing plant damage that simultaneously interferes with transportation and extends delivery times. Companies need to develop backup strategies due to climate-related risk growth which poses severe threats to their operations.
Another environmental risk comes from violating sustainability regulations. If a company dumps waste illegally or releases harmful chemicals, it might face fines or be forced to shut down, which disrupts the entire supply chain.
How to Manage Natural Disaster Risks:
- Have backup suppliers in different locations.
- Store extra inventory to cover delays.
- Use weather tracking systems to anticipate potential disasters.
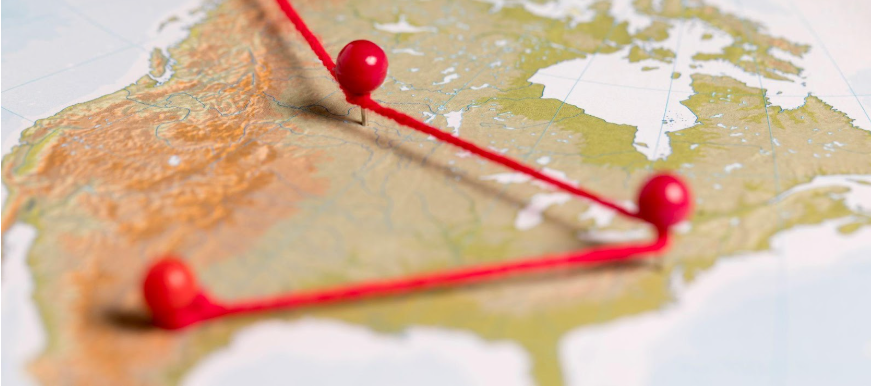
2. Geopolitical Risks
International business operations experience effects from political instability which spreads throughout the world. Various political events such as trade wars together with government policy shifts and national conflicts can result in increased export tariffs and trade barriers and complete supply chain disruptions.
For example, if a country suddenly bans exports of a key raw material, companies depending on that material will struggle to keep production going. In extreme cases, companies might need to shut down factories or find new suppliers quickly.
How to Manage Geopolitical Risks:
- Work with multiple suppliers in different countries to avoid dependency on one location.
- Keep an eye on global news to predict potential trade disruptions.
- Move some manufacturing operations closer to home (a strategy called nearshoring or onshoring) to reduce dependency on politically unstable regions.
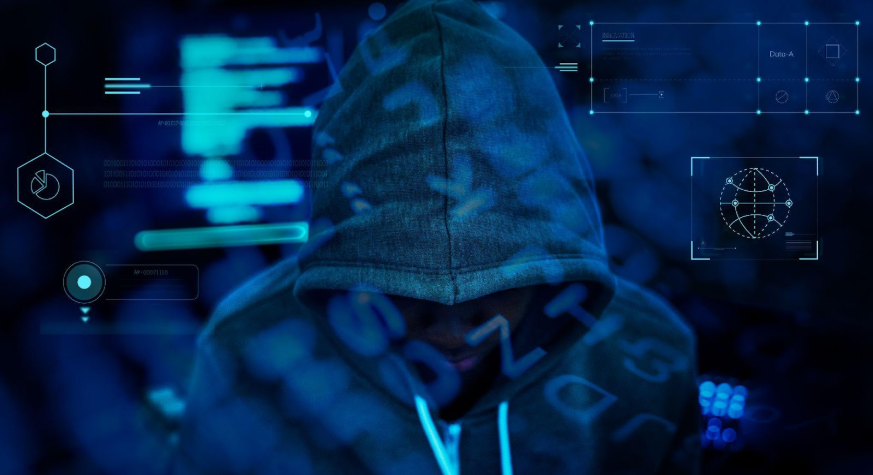
3. Cyberattack Risks
The adoption of technological systems by contemporary businesses exposes them to cyber security threats. IT system attacks from hackers enable thieves to acquire sensitive information while halting business operations and supply chain tampering. When cybercriminals strike a logistics provider’s systems it becomes possible for their deliveries to fail to reach their intended recipients.
Small businesses face higher risks because they often lack strong cybersecurity defenses. If a company’s software provider gets hacked, it can impact every business using that software.
How to Manage Cyberattack Risks:
- Use secure software from trusted vendors.
- Train employees on cybersecurity best practices.
- Have a recovery plan in case of a cyberattack.
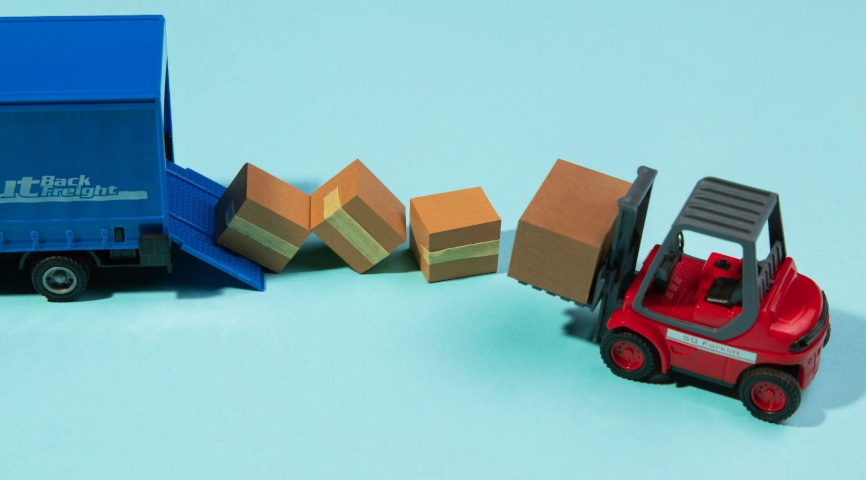
4. Supply Risks
Supply risks emerge when suppliers experience time delays with product delivery while simultaneously delivering poor quality materials and if any of their operations lead to business closure. Operating a bakery while your flour supplier breaks their delivery commitment leads to a complete disruption of your business!
Sometimes, supply risks happen due to shortages in raw materials. If there is a global shortage of a particular component, companies might struggle to meet customer demand.
How to Manage Supply Risks:
- Build strong relationships with multiple suppliers.
- Monitor supplier performance and financial stability.
- Have alternative sources ready in case of emergencies.
Other Common Supply Chain Risks
Besides the major risks mentioned above, there are additional challenges that companies need to watch out for:
- Economic Risks – A financial crisis, inflation, or changes in currency exchange rates can impact supply chains.
- Operational Risks – Machinery breakdowns, IT failures, and worker strikes can slow down production.
- Financial Risks – If a company runs out of cash or loses investor support, it may struggle to pay suppliers.
- Ethical Risks – Using suppliers that engage in unethical practices, such as child labor, can harm a company’s reputation.
- Reputational Risks – A single bad review or scandal can drive away customers.
- Demand Planning Issues – Misjudging customer demand can lead to shortages or excess inventory.
- Human Resource Risks – Employee turnover, lack of skilled workers, or labor shortages can slow down business operations.
- Quality Risks – Poor quality materials or defective products can lead to recalls and financial losses.
How Businesses Can Reduce Supply Chain Risks
Managing risks is all about preparation. Companies that plan for different types of disruptions can recover faster when problems arise. Here are some key strategies:
- Conduct regular audits to check for potential risks.
- Use automation and software to improve visibility and efficiency.
- Train employees to handle unexpected challenges.
- Work with reliable suppliers and have contingency plans in place.
- Invest in cybersecurity to protect digital assets.
By understanding and managing these risks, companies can build stronger and more resilient supply chains. This is a key concept in WGU D471, helping students and professionals navigate the challenges of global supply chains.
In today’s fast-paced manufacturing world, companies must choose between efficiency-driven Lean Manufacturing and flexibility-focused Agile Manufacturing—or strike the perfect balance between the two
Lean vs. Agile Manufacturing: Understanding the Differences For D471 OA 📝
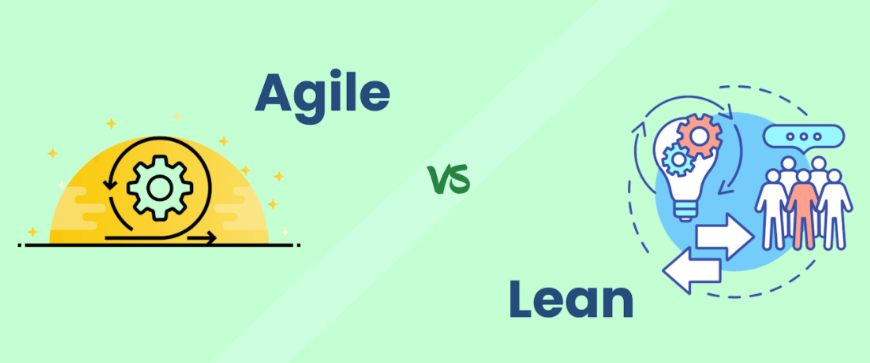
Consumer manufacturers from various parts of the world use diverse methods to both improve productivity and maintain market leadership. Manufacturing organizations commonly implement two different production methods which are Lean Manufacturing and Agile Manufacturing. These two efficiency enhancement methods adopt distinct strategies even though their core objectives differ from one another. The following section gives detailed information about these concepts with simple explanations that make their meaning clear to the reader.
Understanding Lean Manufacturing
Lean manufacturing focuses entirely on maximizing operational effectiveness. The method directs organizations to minimize waste by eliminating unnecessary steps to achieve maximum production efficiency. Companies create their products through the quickest and most affordable methods to maintain superior quality standards. Companies applying lean principles dedicate their efforts to cutting down inventory excess as well as eliminating unnecessary movements and reducing manufacturing delays. The system functions optimally within predictable demand environments due to which enterprises can conduct their operations with minimal waste generation.
A core concept in lean manufacturing is waste reduction, which targets eight major types of waste:
- Transportation – Moving products or materials unnecessarily, leading to increased costs.
- Inventory – Holding more raw materials or finished goods than necessary, which ties up capital.
- Motion – Excess movement of workers or equipment that reduces efficiency.
- Waiting – Delays in production due to bottlenecks or lack of materials.
- Overproduction – Making more products than needed, leading to surplus stock.
- Over-processing – Performing more work than required, using extra steps or complex processes.
- Defects – Errors that require rework or waste valuable materials.
- Unused Talent – Failing to leverage employees’ full potential by not utilizing their skills effectively.
Lean manufacturing applies techniques such as value stream mapping to identify inefficiencies and continuous improvement (Kaizen) to encourage small, ongoing refinements in production processes. These strategies help businesses cut costs, improve quality, and deliver products efficiently.
Understanding Agile Manufacturing
That’s where agile production enters the scene because it stands for flexibility in operations. Agile production systems enable manufacturers to reshape manufacturing output to accommodate shifting customer needs and emerging market patterns as well as emergency market events. The approach of agile manufacturing differs from lean because agility enables successful operation in constantly changing environments.
Key principles of agile manufacturing include:
- Customer Collaboration – Engaging customers throughout the production process to meet their needs.
- Cross-Functional Teams – Encouraging employees from different departments to collaborate for faster problem-solving.
- Quick Iteration Cycles – Using short production cycles to adapt to customer feedback and market changes.
- Flexible Production Systems – Enabling production lines to switch between different products with minimal downtime.
- Decentralized Decision-Making – Allowing teams to make quick decisions without waiting for upper management approval.
Due to their agile capabilities clothing producers can change from making summer clothes to creating winter coats promptly after unexpected weather conditions arise. The company maintains a top position in competition through its fast response which leads to efficient customer demand fulfillment..
Lean vs. Agile: A Side-by-Side Comparison
Feature | Lean Manufacturing | Agile Manufacturing |
Primary Focus | Efficiency and waste reduction | Flexibility and quick response to change |
Production Approach | Standardized, streamlined processes | Customizable, adaptable workflows |
Customer Involvement | Focuses on delivering value efficiently | Actively involves customers in product development |
Speed and Iteration | Continuous improvement over time | Short iteration cycles with frequent updates |
Team Structure | Structured roles and responsibilities | Cross-functional teams for dynamic problem-solving |
Best For | High-volume, predictable production | Custom, unpredictable, or fast-changing demand |
Combining Lean and Agile: A Hybrid Approach
Many businesses use a mix of both lean and agile strategies to get the best of both worlds. They apply lean principles in areas where efficiency is crucial and agile methods in segments that require quick adaptability. For example, an automotive company may use lean practices for mass-producing car models but integrate agile techniques to customize high-end luxury models based on individual customer preferences.
The Role of Technology in Lean and Agile Manufacturing
MES systems enable the monitoring of manufacturing data alongside operational monitoring features that identify issues when they emerge. IoT technology together with intelligent sensors helps identify machine operational performance indicators that predictive maintenance uses to schedule needed repairs before system failure occurs.
Importance For the D471 OA
Modern industry requires companies to follow two essential operational strategies known as Lean Manufacturing and Agile Manufacturing. A core difference emerges between lean strategy which aims to eliminate waste and boost operational efficiency and agile methodology concentrates on agile adaptation and quick responses to changes. Production optimization now combines both manufacturing methodologies within numerous modern companies. The key knowledge of these strategies becomes vital for enterprises that want to stay relevant in current high-speed markets.
This is a key concept in WGU D471, helping students and professionals master supply chain management and modern manufacturing techniques. By applying these principles, businesses can enhance efficiency, reduce costs, and improve their ability to adapt to ever-changing customer demands.
Tired of reading blog articles?
Let’s Watch Our Free WGU D471 Practice Questions Video Below!
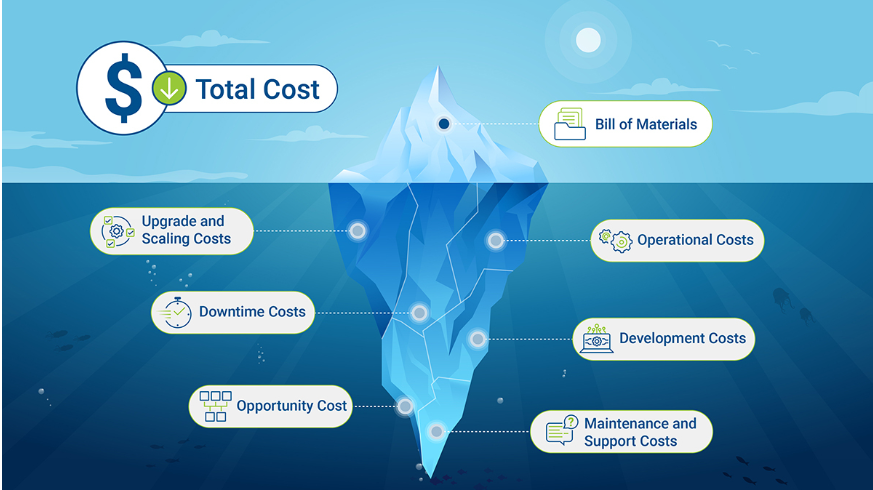
Understanding Total Cost of Ownership (TCO) in Supply Chain Management For D471 OA📖
A business deal for purchasing goods or services requires customers to pay more than just the agreed price because of additional expenses. Businesses understand the entire investment by using Total Cost of Ownership (TCO) to calculate all spending linked to products from start to finish. Companies must evaluate both purchase price along with operational expenses maintenance costs downtime occurrences and end-of-life disposal to determine TCO. Organizations need complete TCO understanding to create well-informed financial decisions while improving their supply chain operations.
Breaking Down Total Cost of Ownership
TCO includes full acquisition expenses together with all operational and support costs from the beginning to the end of product life expectancy. Businesses need to recognize both the purchase price together with other concealed expenses that dramatically affect profitability. Companies better invest after understanding TCO because they learn to predict future expenses beyond their initial purchase expenses.
Key Components of TCO
A comprehensive analysis of TCO includes several cost elements, each contributing to the overall expense of a product or service:
- Acquisition Costs: Total acquisition expenses consist of the original item or service payment made at the moment of purchase. The acquisition costs represent just the biggest expense type but do not make up the majority of total expenditures.
- Operational Costs: These are the expenses involved in using the product, including energy consumption, labor, and routine operating costs.
- Maintenance Costs: Products require servicing, repairs, and potential upgrades over their lifetime, all of which contribute to the TCO.
- Downtime Costs: Unexpected failures or breakdowns can halt production, leading to revenue losses and increased expenses for urgent repairs.
- Disposal Costs: At the end of a product’s life, companies must pay for recycling, replacing, or disposing of it, adding to the total expense.
- Supply Chain Integration Costs: The implementation of new products in supply chains requires companies to allocate funds for system modernization together with security protection measures while also covering training expenses for employees.
All finite factors enable businesses to develop enhanced estimates about how much it costs to truly use and own products.
Why TCO Matters in Procurement
Many businesses fall into the trap of choosing products based solely on the lowest upfront cost. However, a cheaper product may lead to higher maintenance costs, frequent repairs, and downtime, ultimately making it more expensive in the long run. That’s where TCO analysis helps—by shifting the focus from price to long-term value.
The Role of TCO in Smarter Procurement Decisions
TCO is an essential metric in procurement because it ensures that companies select products and services based on their actual financial impact rather than just the initial purchase cost. Here are some ways businesses benefit from TCO analysis:
- Better Vendor Selection: Companies can evaluate suppliers not just based on price, but also on long-term reliability, maintenance, and support.
- Cost Reduction Strategies: Identifying areas where costs can be minimized, such as reducing downtime or optimizing energy usage.
- Improved Budget Planning: TCO analysis helps in forecasting future expenses and preventing unexpected financial burdens.
- Enhanced Risk Management: Risk Management Is Improved Through Security Risk Assessment Compliance Checks and Operational Impairment Evaluations During Product Selection.
Calculating Total Cost of Ownership
Calculating TCO involves assessing both the visible and hidden costs associated with a purchase. Businesses typically follow these four main steps:
- Identify All Costs: List every cost associated with a product, from acquisition to disposal.
- Assign Monetary Values: Estimate and assign a value to each cost component.
- Sum Up Costs: Add up all expenses to determine the full ownership cost.
- Calculate Annual TCO: Divide the total cost by the expected lifespan of the product to understand annual expenses.
Using TCO calculators and software tools can simplify this process, ensuring businesses get accurate insights into their investment decisions.
TCO in Supply Chain Optimization
A well-calculated TCO analysis helps businesses optimize supply chain operations by eliminating unnecessary expenses and improving cost efficiency. Here’s how companies use TCO in supply chain management:
- Optimizing Inventory Management: Reducing storage costs, minimizing stockouts, and ensuring efficient replenishment.
- Enhancing Supplier Collaboration: Working with suppliers who offer lower long-term costs, even if their initial pricing is higher.
- Improving Transportation Decisions: Choosing transportation modes that minimize total cost rather than just focusing on fuel expenses.
Importance For the D471 OA
Businesses use the TCO analysis tool for making strategic purchasing decisions that surpass the single evaluation of product costs. Organizations secure efficiency while minimizing risks and boosting profitability through Total Cost of Ownership understanding in vendor selection supply chain management and procurement operations.
This concept is crucial in WGU D471, where students learn to analyze and apply financial strategies for supply chain management. By mastering TCO, professionals can make smarter, more sustainable business decisions in the competitive global marketplace.
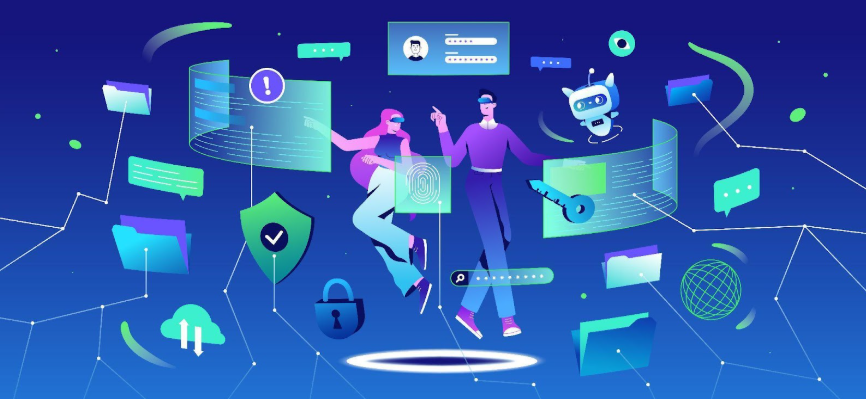
Final Thoughts: Mastering WGU D471 OA for Supply Chain Success📖
Supply chain management extends beyond simple product delivery because it involves both risk forecast and operational excellence together with financial strategy development. People practicing supply chain need to understand natural disaster threats to global networks plus both lean and agile manufacturing systems as well as Total Cost of Ownership (TCO) principles for success in the profession.
The essential areas you need to master for your WGU D471 OA course include these topics. Knowledge about supply chain risks enables you to predict industry disruptions while they are still in the future. You will achieve market adaptability through the proper implementation of lean or agile production methods. A complete understanding of TCO enables you to make affordable decisions that extend past product costs.
These ideas represent actual business methods that industry organizations put into action daily. Use the studying period to apply lessons learned because this will boost your confidence during your final evaluation. Best of luck on your WGU D471 OA—you’ve got this!
