WGU D469 OA Study Guide - 2025 | Mastering Process Improvement📖
Picture this: During a running competition, each footstep contributes to methodical workflow formation. When you run with your footwear tied jointly it creates challenges for your movement. Not the best start, right? Process improvement attempts without proper tools often result in the same situation. Your process improvement toolkit includes:
- Six Sigma DMAIC: A structured, data-driven methodology used for improving processes, DMAIC stands for Define, Measure, Analyze, Improve, and Control. It’s designed to identify and remove the causes of defects, ensuring processes operate at optimal efficiency.
- How to Use SIPOC Diagrams: SIPOC stands for Suppliers, Inputs, Process, Outputs, and Customers. It’s a high-level tool used to map out processes in a simple, visual format, helping teams understand the flow of materials and information across a process and ensuring all relevant components are considered.
- How to Use Cause-and-Effect Diagram: Also known as the Fishbone or Ishikawa diagram, this tool helps identify the root causes of problems within a process. By categorizing potential causes, teams can systematically address and eliminate sources of issues, improving overall quality.
When you reach the end of this guide you will gain the skills required to solve process issues at every size level. Let’s work on transforming process enhancement from endless looping into the swift achievement of final goals that bring effective results!
How to Use This Guide for the WGU D469 OA Exam?📖
The D469 Quality, Continuous Improvement, and Lean Six Sigma OA exam at WGU evaluates your understanding of quality management tools, process improvement methods, and Lean Six Sigma principles. This guide simplifies the key concepts of Six Sigma DMAIC, how to use SIPOC diagrams, and how to use cause-and-effect diagrams to help you grasp the topics tested in the exam.
We also provide exam-style questions and practical applications to ensure you’re fully prepared for the questions on the WGU D469 OA exam.
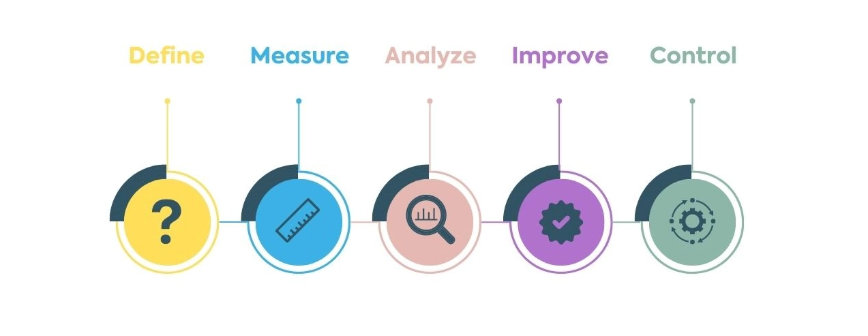
Understanding Six Sigma DMAIC For D469 OA 📝
Introduction to Six Sigma DMAIC
Six Sigma delivers a solution-based procedure that enables organizations to detect and remove productive issues from their operational applications. Six Sigma concentrates on streamlining organizational operations and eliminating resource wastage while delivering superior product results. The process tool used most commonly within Six Sigma projects is the DMAIC method.
DMAIC introduces five steps: begin with Define and end with Control, and include Measure, Analyze, and Improve. DMAIC delivers organized solutions for every step of process problem resolution within organizations. The following explains the fundamental stages for a clear understanding of its features.
1. Define – Understanding the Problem
The first step in the DMAIC process is to Define the problem. This means understanding what issue needs to be addressed and why it’s important. To get started, ask these questions:
- What’s the problem?
- Who is affected by this problem?
- What is the goal or desired outcome?
At this time you build a project charter serving as a project navigation guide. A project charter includes all essential project information including problem description with defined goals and team assignment details.
Example: Imagine a company’s customer service department is getting a lot of complaints about long wait times. The team would define the problem as “long wait times” and aim to reduce them to a specific target, such as under 5 minutes.
2. Measure – Collecting Data
Process definition follows a dual-step procedure beginning with performance measurement of current operations. The collection of data to determine the current operational status is happening at this point.
The measurement phase for customer service team performance collects statistics that reveal how much time customers need to wait until their calls start being answered.
During this step, you might use tools like data charts and checklists to record the data. The goal is to measure the current state of the process so you can compare it later after improvements have been made.
3. Analyze – Understanding the Root Cause
Your next step involves data analysis after you have obtained your data measurements. During this analytical phase, you use data to probe why the existing problem has occurred. The exercise centers on locating the fundamental source instead of concentrating on observable manifestations.
Some common tools used in this phase include Pareto charts (which help you see the most common causes of problems) and fishbone diagrams (also known as Ishikawa diagrams, which help identify different potential causes in categories like people, equipment, processes, etc.).
Example: A data analysis reveals that extended waiting periods result mainly from inadequate staffing of customer service representatives throughout peak usage hours.
4. Improve – Finding Solutions
Analysis of the root cause allows teams to start implementing process improvements. During this step, teams brainstorm and develop strategies that resolve the detected problem. The process involves testing separate solutions to determine which produces optimal results.
You need to find vital process enhancements which result in significant process progress. The proposed solutions aim to improve outcomes by modifying operational flows but also by adding staff or investing in updated technology. The measurement of performance improvements allows us to see whether the changes benefit the process.
Example: The team could decide to add more agents during peak times, introduce automated systems for handling routine inquiries, or streamline the process of answering calls.
5. Control – Ensuring the Improvements Last
The final step in DMAIC is Control. This is about making sure the improvements you’ve made stay in place over time. It’s important to have a system in place to monitor the process and prevent the problem from happening again.
During this phase, you might use control charts to track performance, set up new standard operating procedures (SOPs), or create training materials for employees.
Example: After adding more agents and streamlining processes, the team can use performance charts to monitor wait times daily. They might also create a new schedule that ensures there are always enough agents during peak hours.
Why DMAIC is Important For D469 OA
DMAIC represents a potent process enhancement methodology. Organizations achieve systematic problem-solving and quality enhancement through the execution of these five defined steps. Productivity and satisfaction improvements as well as waste reduction are all achievable through DMAIC’s defined methodology for resolving organizational problems.
WGU D469 OA students must know DMAIC methodology since this tool delivers a distinct structure to handle practical business issues faced at work. Through Six Sigma tools, students along with professional workers learn to optimize organizational processes for effective results.
Now that we’ve explored the DMAIC method for improving processes, let’s dive into SIPOC diagrams, a powerful tool for mapping out and visualizing the key components of any process.
How to Use SIPOC Diagrams For D469 OA📝
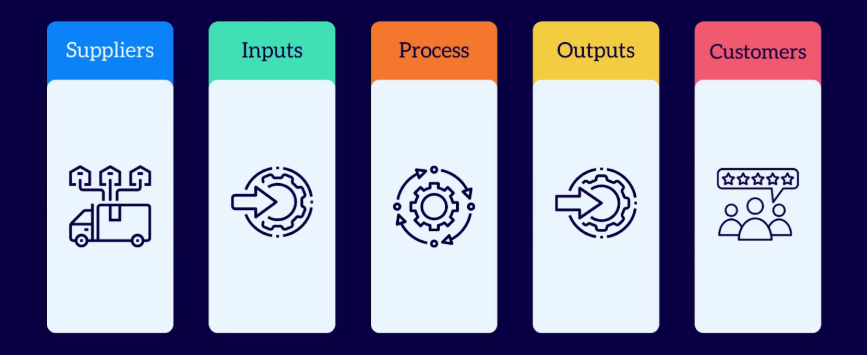
Introduction to SIPOC Diagrams
In the world of process improvement, one of the most useful tools for understanding a process from start to finish is the SIPOC diagram. SIPOC stands for Suppliers, Inputs, Processes, Outputs, and Customers. As an executive-level assessment tool, it enables teams to view every functional aspect involved in a specific process.
SIPOC diagrams serve as vital tools for project initiation in Six Sigma and Lean because they create a process overview to aid process improvement identification. Here we will analyze SIPOC components through an explanation of how they help establish process mapping.
1. Suppliers – Who Provides the Inputs?
Business relationships deemed suppliers represent the first essential element in building a SIPOC diagram. Processes obtain essential components from suppliers which may include people or organizations and technological platforms. External vendors and internal departments and machines supply both raw materials and data resources and additional assets required by the process.
The Suppliers part of a SIPOC diagram shows organizing all direct process elements. Identifying suppliers helps you recognize your input sources making it easier to confirm their reliability together with their high quality standards.
Example: When creating custom t-shirts the various suppliers range from fabric suppliers to printing companies and equipment manufacturers.
2. Inputs – What Resources Are Needed?
The next part of the SIPOC diagram is Inputs. Inputs are the resources, materials, or information required to carry out the process. This could include raw materials, equipment, data, or human resources. These are the things that suppliers provide to enable the process to run.
Listing inputs helps teams focus on what they need to get the job done and ensure that all the necessary resources are available before starting the process.
Example: In the t-shirt-making process, inputs could include the fabric, printing designs, and printing machines.
3. Process – What Are the Key Steps?
SIPOC’s Process section contains the step-by-step activities through which inputs convert into final outputs. The series of needed implementation steps appear within this central section. This stage of the process demonstrates its main steps before getting into specific tasks.
In a SIPOC diagram, the process should be broken down into a few clear steps to show the flow of work. These steps might include tasks like assembly, processing, quality checks, etc.
Example: For the t-shirt-making process, the key steps might include designing the shirt, cutting the fabric, printing the design, and then packaging the shirts.
4. Outputs – What Are the Results of the Process?
After the process has been completed, it produces Outputs. Outputs are the final products, services, or results that the process delivers. These outputs are what the customer ultimately receives or what the organization uses to achieve its goals.
In a SIPOC diagram, it’s important to identify the outputs to understand how successful the process is in meeting its objectives. This helps in analyzing whether the outputs align with customer expectations or business goals.
Example: In the t-shirt process, the outputs would be the finished t-shirts, ready for sale.
5. Customers – Who Receives the Outputs?
The last essential element within SIPOC diagrams grants attention to Customers. All processes conclude with customer entities who receive generated outputs. The components of this model exist either inside organizational boundaries or beyond them. The process recipients include those who directly use products and services as well as intra-organizational departments and outside businesses that require finished outputs.
By identifying customer groups you can determine their requirements and expectations. To guarantee process alignment with customer priorities companies must determine which values matter most to customers whether these are quality delivery speed or cost-effectiveness.
Example: The target audience of the t-shirt process includes both retail outlets that distribute the shirts alongside individual buyers who purchase online.
How to Create a SIPOC Diagram
Now that we’ve gone over the components of SIPOC, let’s discuss how to create one. It’s easy to get started with a SIPOC diagram, and it doesn’t require a lot of detailed data at first. Here’s a simple process to follow:
- List the suppliers: Start by identifying the suppliers that provide the resources for the process.
- Identify the inputs: Then, list the inputs that are required for the process.
- Map out the process: Write down the major steps in the process.
- Determine the outputs: Identify the final product or result of the process.
- Identify the customers: List the people or organizations that will receive the outputs.
You can use a simple table to organize your SIPOC diagram:
Suppliers | Inputs | Process | Outputs | Customers |
Supplier A | Input 1 | Step 1 | Output 1 | Customer 1 |
Supplier B | Input 2 | Step 2 | Output 2 | Customer 2 |
Supplier C | Input 3 | Step 3 | Output 3 | Customer 3 |
By using a SIPOC diagram, you can clearly see the relationships between each part of the process, which helps in identifying areas where improvements can be made.
Why SIPOC is Useful For D469 OA
SIPOC diagrams are essential tools in the world of quality improvement. They help teams:
- Visualize the process: A clear high-level process view emerges through the mapping of each SIPOC element.
- Identify inefficiencies: Through SIPOC organizations can locate operational gaps and deficiencies for subsequent improvement actions.
- Align teams: STOPEC enables every stakeholder to comprehend the process pathway through its visual framework which defines their responsibilities while outlining supplier and customer requirements.
D469 OA students alongside students conducting process improvement projects should use SIPOC diagrams early in their projects because they help establish shared project understanding.
After mastering SIPOC diagrams to map out processes, let’s move on to the Cause-and-Effect diagram, a critical tool for uncovering the root causes of problems within those processes.
Tired of reading blog articles?
Let’s Watch Our Free WGU D469 Practice Questions Video Below!
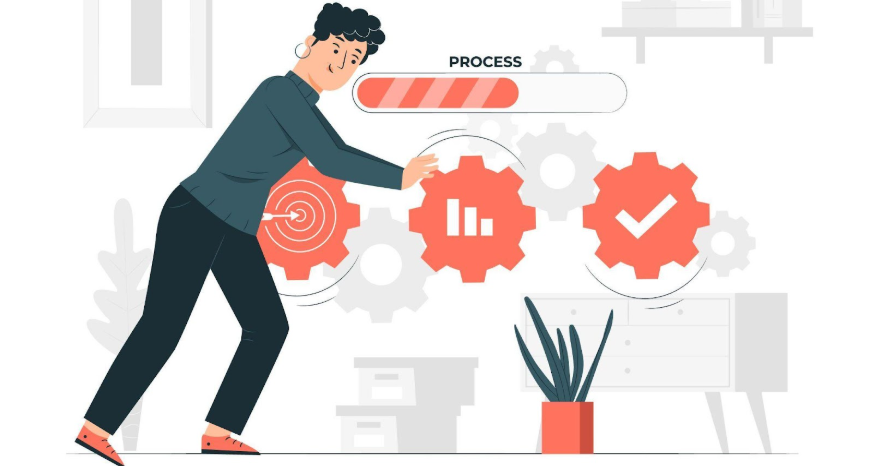
How to Use Cause-and-Effect Diagrams For D469 OA📖
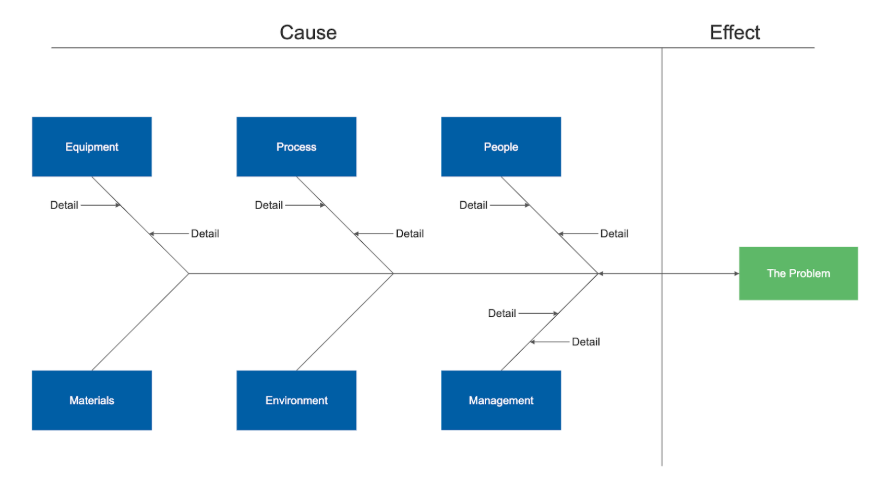
Introduction to Cause-and-Effect Diagrams
Efforts to solve problems often struggle with the identification of basic cause elements. Identifying the multiple causes behind each issue creates a feeling of overwhelming complexity when you try to understand what’s going wrong. This is where a Cause-and-Effect diagram, also known as an Ishikawa diagram or fishbone diagram, comes in handy.
A Cause-and-Effect diagram allows stakeholders to create visual maps that identify different problem causes. Such tools simplify complex matters into components which lets you easily discover the main causes. This tool allows users to identify problem origins and develop required solutions.
What is a Cause-and-Effect Diagram?
A Cause-and-Effect diagram is a visual tool that shows the relationship between a problem (the effect) and the possible causes that lead to it. The diagram looks like a fishbone, with the “head” being the problem and the “bones” representing different causes that contribute to the problem.
This diagram serves as a method for organizing evaluations of various possible causes for specific issues. You can identify all necessary causes that lead to problems during process improvement initiatives using this diagram which offers insights beyond mere symptoms.
The Structure of a Cause-and-Effect Diagram
The Cause-and-Effect diagram has a simple structure that makes it easy to use:
- The Head: The effect, or the problem, is written at the far right, like the “head” of a fish.
- The Spine: This is the line that connects the problem to the potential causes.
- The Bones: These represent categories of causes that could be contributing to the problem. Each “bone” can be broken down further into more specific causes.
The categories of causes can vary depending on the process you’re analyzing, but the most common ones are:
- People: Human factors like skills, knowledge, and communication.
- Process: Steps or procedures that might be causing the issue.
- Materials: The raw materials, supplies, or equipment used in the process.
- Machines: Tools, machines, and technology used in the process.
- Environment: The physical or external factors that might be affecting the process.
- Measurement: Problems related to data, metrics, or measurements.
How to Create a Cause-and-Effect Diagram
Here’s a simple, step-by-step process for creating a Cause-and-Effect diagram:
- Identify the Problem (Effect): Write down the problem you’re trying to solve at the “head” of the fish. Be specific about what is happening.
Example: Let’s say the problem is “Low customer satisfaction.” - Brainstorm Possible Causes: Think about all the factors that could be contributing to the problem. Write these causes along the “bones” of the fish. Start with the major categories like People, Process, Materials, etc., and break them down into more detailed causes.
Example: For “Low customer satisfaction,” possible causes might include:- People: Untrained staff, lack of communication skills.
- Process: Complicated return process, slow response time.
- Materials: Poor quality products.
- Machines: Outdated technology.
- Break Down Each Cause: Under each category, list more specific causes that could be contributing to the problem.
Example: Under People, you might break it down further to “Lack of training on new products” or “Poor attitude from customer service representatives.” - Analyze and Identify Root Causes: After you build the diagram you should use it to evaluate the possible causes and recognize which ones play the biggest role in creating the issue. Goal-setting must center on original problem elements instead of dealing with observable effects first.
Why Use Cause-and-Effect Diagrams?
Cause-and-Effect diagrams are a powerful tool for problem-solving for several reasons:
- Clarity: These tools guide users to see complicated challenges while separating them into parts that become much more workable entities.
- Collaboration: Teams use these diagrams as a brainstorming method to identify causes while working together to solve problems from different angles.
- Root Cause Identification: To determine accurate root causes you must investigate past the surface symptoms thus preventing useless expenditure of time on inadequate solutions.
- Systematic Approach: A systematic structure provides you with a method to handle problems by assuring that you investigate all relevant elements and origin factors.
Studying WGU D469 OA through a Cause-and-Effect diagram will lead students to approach problems systematically while providing better organization to their methods.
Example of a Cause-and-Effect Diagram
Let’s look at an example to better understand how to use a Cause-and-Effect diagram. Imagine you’re working on improving a customer service process that has a high level of complaints. Your goal is to identify the causes of dissatisfaction.
You would first define the problem: A high number of customer complaints. Then, break the problem into categories such as People, Process, and Materials.
- People:
- Lack of training
- Poor communication skills
- Process:
- Slow response time
- Complicated complaint resolution process
- Materials:
- Insufficient customer service tools
- Outdated FAQ section on the website
As you brainstorm, you will continue breaking down each category into more specific causes until you have a clear view of what’s contributing to the problem.
Using Cause-and-Effect For D469 OA
WGU D469 OA projects and real-world process improvement initiatives succeed with the use of Cause-and-Effect diagrams because these tools help teams determine genuine problem roots. Both Six Sigma and Lean require identifying the fundamental sources to produce meaningful ongoing improvements.
After building your diagram and identifying root causes you can start designing targeted solutions that address precise problems which leads to better problem-solving outcomes.
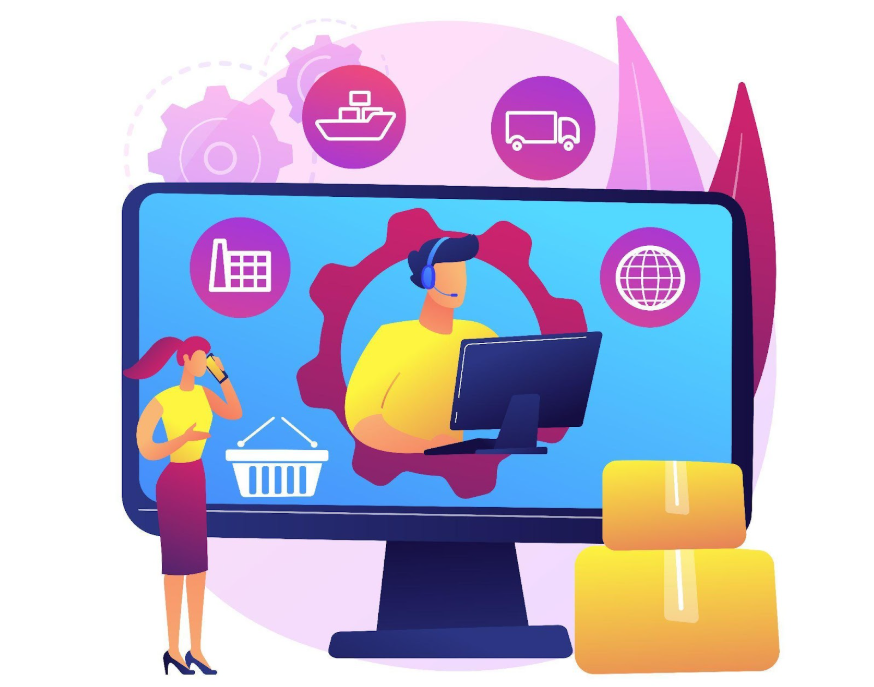
Wrapping Up Process Improvement: Your Key Tools for WGU D469 OA Success📖
And there you have it! After our detailed exploration of core Six Sigma DMAIC protocols combined with SIPOC diagrams and Cause-and-Effect diagrams, we need to absorb this knowledge until it becomes second nature. Believe us when I say these tools represent significant instruments beyond WGU D469 OA because they let you solve process problems expertly.
Mastering implementation of these tools will provide necessary support during your final WGU D469 objective assessment work so invest effort into detailed understanding and practical application methods. Although initially daunting the more times you rehearse these skills the greater your self-assurance becomes before the actual demonstration. Breathe deeply for success followed by intense study because you will crush the OA work with flying colors.
Good luck, and may your process improvement journey be smooth and full of success. You’ve got this!
